Working on elevated platforms, whether in construction, maintenance, or warehouse settings, poses unique safety challenges. Each year, incidents related to falls and missteps on elevated surfaces account for a significant percentage of workplace injuries. Implementing a robust safety protocol not only protects employees but also reduces liability and downtime for companies. Below are eight safety essentials every company should emphasize to ensure the safety of employees working on elevated platforms.
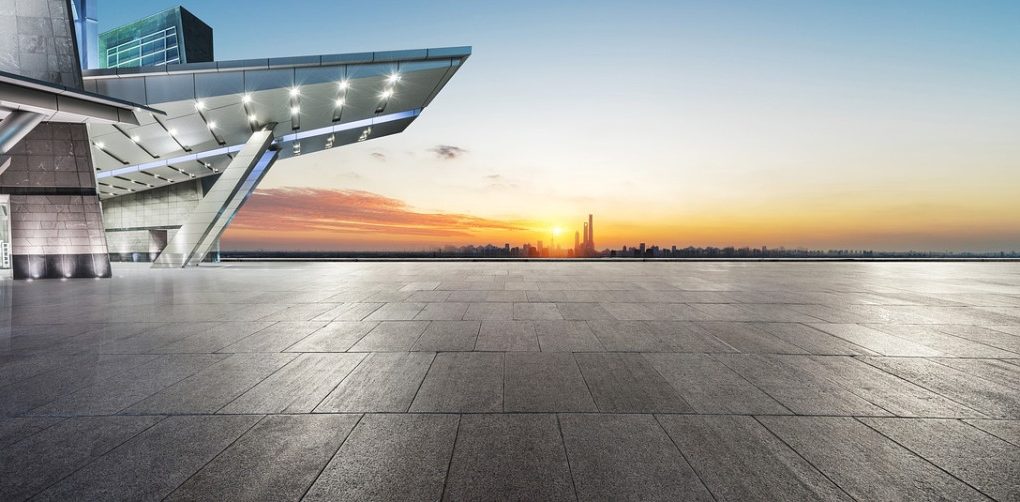
1. Personal Protective Equipment (PPE)
Personal protective equipment is crucial for employees working at heights. Helmets, safety harnesses, lanyards, and sturdy footwear are essential items that can prevent serious injuries or even save lives. For instance, a properly fitted harness connected to a reliable anchor point can arrest falls in case of a misstep. Employees should be educated on the correct use, care, and limitations of their PPE to ensure they are fully protected while on elevated platforms.
Regular inspections of PPE are essential. Faulty or worn-out equipment can lead to disastrous outcomes, so it’s critical that companies make PPE checks part of their regular safety routine. Companies should also provide training on when to replace equipment to maintain its effectiveness.
2. Comprehensive Training Programs
Effective training is the foundation of any robust safety program. Employees working at heights must understand the hazards associated with elevated work and how to minimize their risk. Training should cover topics such as fall arrest systems, the importance of balance, and situational awareness on narrow or uneven platforms.
Incorporating hands-on practice is essential. Theory-based lessons only go so far, but practical training allows employees to experience simulated situations, making them more prepared and confident on the job. Additionally, refresher courses should be offered regularly to keep safety protocols top of mind.
3. Conducting Routine Equipment Inspections
Platforms, ladders, and scaffolding used in elevated work need to be inspected routinely for signs of wear, corrosion, or structural damage. Even a small fault in a piece of equipment can escalate into a major safety issue. Daily pre-work checks and scheduled maintenance are essential to keeping equipment reliable and safe for use.
Inspections should include all structural components, fasteners, and guardrails, ensuring everything is secure and in good condition. Companies should keep records of these inspections and follow up on any identified issues promptly. This level of diligence helps reduce the risk of equipment-related accidents.
4. Implementing Clear Signage and Barriers
Visual cues like signage and barriers are important for keeping employees aware of their surroundings on elevated platforms. Signs should indicate the maximum weight capacity of platforms, designated entry and exit points, and any additional safety instructions relevant to the platform’s location and use. Barriers, including guardrails and toe boards, help prevent accidental slips or falls by clearly marking platform edges and preventing items from being kicked off.
Additionally, areas below elevated workspaces should be cordoned off to protect other workers from falling debris. Clear signage and barriers serve as constant reminders of the potential hazards present and help maintain a safety-conscious mindset.
5. Specialist Training and Consulting Services
Companies should consider investing in external training and consulting services that specialize in working at heights. Many firms provide tailored programs that cover essential safety skills, legal compliance, and equipment handling techniques. These services often extend to providing on-site assessments, manpower for high-risk jobs, and consultations on industry best practices.
Incorporating these resources into your safety program can significantly elevate safety standards. Employees who receive comprehensive, specialized training are better prepared for high-risk situations. In this context, obtaining a working at heights ticket benefits workers, as it certifies that they have received professional, high-quality training suited to elevated work environments. By choosing a reputable provider, companies can ensure that their workforce is well-equipped with the knowledge and skills necessary for safe elevated platform operations.
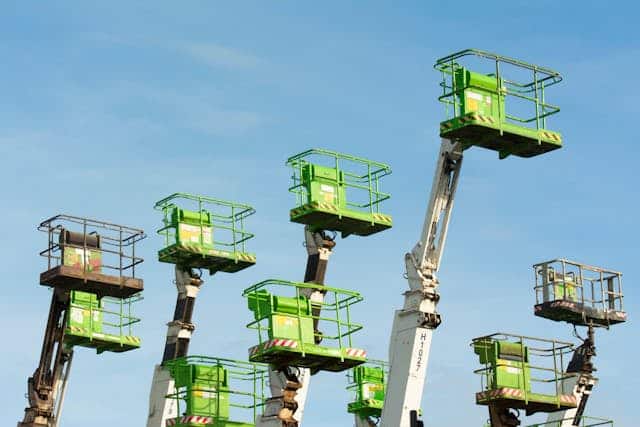
6. Safe Use of Tools and Equipment
Tools and materials used on elevated platforms pose a unique risk if not handled properly. A dropped tool can cause serious harm to individuals below or create balance issues for workers on the platform. Employees should be trained in the secure handling and storage of tools to prevent accidental drops. Lanyards for tools, for instance, can be attached to workers to reduce the risk of items falling from heights.
Additionally, workspaces should be kept organized to avoid clutter that could lead to tripping hazards. Clear, designated storage areas for tools and materials help keep the platform orderly, which is essential for maintaining a safe working environment.
7. Weather Awareness and Environmental Conditions
Working at heights is particularly sensitive to environmental conditions. Wet, icy, or windy conditions can make elevated platforms dangerously slippery or unstable. Employees and supervisors need to stay informed about weather conditions and assess how they may impact safety. If the platform surface is slippery or the wind is too strong, it may be safer to delay work until conditions improve.
Regular checks on weather forecasts and immediate adjustments to the work schedule demonstrate a company’s commitment to employee safety. Emergency protocols should be in place to help workers evacuate elevated platforms safely in the event of sudden adverse weather conditions.
8. Emergency Preparedness and Rescue Plans
Every company must have a well-rehearsed emergency plan for elevated work scenarios. This plan should cover various situations, including falls, equipment malfunctions, and severe weather. Employees must know how to respond to different emergencies, such as using ladders to evacuate or activating a fall arrest system in case of a fall.
Incorporating regular drills into the workplace routine helps employees internalize these emergency procedures. Having a rescue plan ensures that, in the unfortunate event of a fall or accident, workers are promptly attended to, minimizing the risk of injury. Quick responses and well-planned procedures are critical to workplace safety and can make a significant difference in the outcome of emergencies.
Safety is paramount for employees working on elevated platforms. Implementing strong safety measures—from PPE and thorough training to regular inspections and environmental awareness—creates a secure environment where employees feel protected and valued. Each safety measure discussed is a building block toward preventing accidents and ensuring that elevated work is performed responsibly and effectively. Companies that invest in specialist training and consulting services, demonstrate their commitment to the well-being of their workforce, equipping them with the skills and knowledge they need to perform high-risk tasks safely.
Ultimately, a proactive approach to safety doesn’t just protect employees but also enhances operational efficiency by minimizing accidents and downtime. This commitment to safety cultivates a culture of responsibility and professionalism, where everyone from management to frontline workers prioritizes their well-being and that of their colleagues. Elevated platform safety is not only about compliance but about fostering a workplace where employees feel secure and empowered to do their best work, no matter the height. By integrating these safety essentials, companies can build a resilient workforce capable of handling elevated tasks with confidence and care.