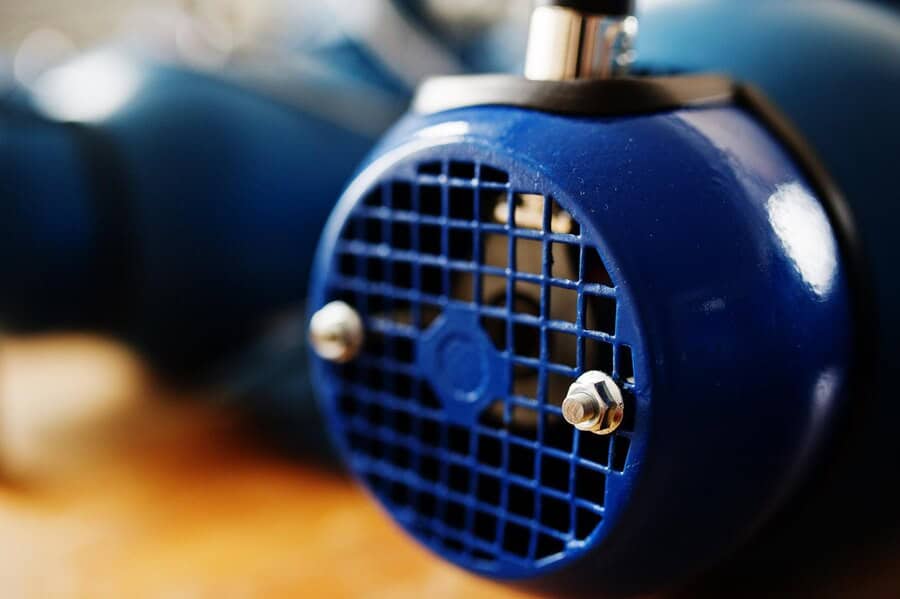
Industrial pumps are essential components across various industries, including construction, manufacturing, wastewater management, and more. These pumps serve the critical function of moving liquids, slurries, and gases from one place to another, enabling processes that are vital to production and operations. The right pump for a specific application ensures efficiency, reliability, and cost-effectiveness. With numerous types of pumps available, it’s important to understand the different categories and their uses. In this article, we’ll break down the main types of industrial pumps, their functions, and where they are most commonly applied.
Slurry Pumps
Slurry pumps are specifically designed to move liquids containing solid particles, such as sand, gravel, and mining byproducts. These pumps are typically heavy-duty and can handle abrasive materials without significant wear. Slurry pumps are essential in industries like mining, construction, and wastewater treatment, where moving thick, solid-laden fluids is a regular task.
Slurry pumps are usually centrifugal in design, but they come with reinforced components that allow them to handle the harsh conditions presented by slurries. They are available in different configurations, including horizontal, vertical, and submersible designs, depending on the application’s specific needs.
For heavy-duty applications involving slurries or high-solids content, it is important to choose a pump that can withstand the wear and tear associated with these materials. Many industries turn to specialized pumps from EddyPump.com and other reputable pump and dredge equipment manufacturers who are known for their ability to handle abrasive slurries with minimal maintenance. Their offered solutions emphasize the importance of selecting pumps tailored precisely to the operational demands, ensuring uninterrupted and reliable service.
Centrifugal Pumps
Centrifugal pumps are among the most widely used types of pumps in industrial settings. These pumps work by using a rotating impeller to generate centrifugal force, pushing fluid outward from the center of rotation and through the pump’s discharge outlet. Centrifugal pumps are known for their simplicity, durability, and ability to handle a wide range of liquids, including water, chemicals, and slurries.
One of the key advantages of centrifugal pumps is their ability to handle high flow rates, making them ideal for applications where large volumes of liquid need to be moved quickly. Common uses include water supply, wastewater treatment, chemical processing, and power generation. However, centrifugal pumps perform best when handling low-viscosity fluids and may struggle with highly viscous or thick slurries.
There are several subtypes of centrifugal pumps, including single-stage, multi-stage, and axial-flow pumps. Single-stage centrifugal pumps are suited for general-purpose applications, while multi-stage pumps are used when higher pressure is required. Axial-flow pumps, on the other hand, are often used in applications where high flow rates at low pressure are needed, such as irrigation and flood control.
Positive Displacement Pumps
Positive displacement pumps work by trapping a fixed amount of fluid and forcing it through the discharge pipe. Unlike centrifugal pumps, which rely on speed to move liquids, positive displacement pumps are designed to move a specific volume of liquid with each cycle, making them ideal for applications requiring precise flow control.
These pumps are highly effective at handling high-viscosity liquids, such as oils, chemicals, and slurries, and they can maintain consistent flow rates even with variable pressure conditions. This makes them valuable in industries like food and beverage production, oil and gas, and chemical manufacturing.
There are two main categories of positive displacement pumps: reciprocating and rotary. Reciprocating pumps, like piston and diaphragm pumps, use a back-and-forth motion to move fluid, making them excellent for high-pressure applications. Rotary pumps, such as gear and screw pumps, use rotating mechanisms to move fluid and are well-suited for handling thicker liquids. Each type of positive displacement pump offers unique advantages, depending on the application’s specific requirements.
Diaphragm Pumps
Diaphragm pumps, a subtype of positive displacement pumps, use a flexible diaphragm to move liquids. The diaphragm is pushed and pulled by a piston or motor, creating suction and discharge to move the fluid. Diaphragm pumps are highly versatile and are especially useful in applications requiring a pump to handle aggressive chemicals, abrasive slurries, or highly viscous liquids.
One of the standout features of diaphragm pumps is their ability to provide a leak-free pumping solution, making them ideal for handling hazardous or corrosive materials. These pumps are commonly used in industries such as chemical processing, pharmaceuticals, food and beverage, and wastewater treatment. Additionally, diaphragm pumps can handle solids-laden liquids without clogging, which makes them suitable for moving sludge or slurry in environmental applications.
Another benefit of diaphragm pumps is their ability to run dry without being damaged, which is not the case for many other types of pumps. This feature makes them highly reliable and long-lasting in situations where continuous operation is required, even in less-than-ideal conditions.
Gear Pumps
Gear pumps, another type of positive displacement pump, are used primarily for moving high-viscosity fluids such as oils, adhesives, and chemicals. These pumps operate by using rotating gears that mesh together to create pockets of fluid, which are then moved through the pump as the gears turn. Gear pumps are known for their ability to handle high-pressure applications and their reliability in maintaining a consistent flow rate.
There are two main types of gear pumps: internal and external. Internal gear pumps use a smaller gear within a larger one, while external gear pumps use two identical gears that rotate against each other. Both designs are effective for handling thick fluids and are commonly used in industries like oil and gas, chemical manufacturing, and food processing.
Gear pumps are highly efficient and can maintain their performance even in high-pressure environments, making them suitable for tasks that require the steady and accurate movement of viscous liquids. However, they are less suitable for handling abrasive materials, as the gears can wear down over time when exposed to solids or slurries.
Peristaltic Pumps
Peristaltic pumps, also known as hose pumps, work by compressing and releasing a flexible hose or tube to move fluid through the system. As the hose is compressed by rollers, the fluid inside is pushed along, and as the rollers release, new fluid is drawn into the hose. This design allows for precise flow control and is particularly effective for handling delicate, corrosive, or viscous fluids.
Peristaltic pumps are frequently used in medical, pharmaceutical, and food processing applications due to their gentle handling of fluids and their ability to avoid contamination. Because the fluid only comes into contact with the hose, peristaltic pumps are ideal for sterile environments where cleanliness is paramount.
These pumps are also excellent for handling abrasive slurries, as there are no moving parts that come into direct contact with the fluid. This makes them useful in mining, wastewater treatment, and chemical processing, where abrasive materials are commonly handled. Another advantage of peristaltic pumps is their self-priming ability, meaning they can start pumping without the need for pre-filling or priming the system.
Screw Pumps
Screw pumps, also known as screw spindle or auger pumps, are a type of positive displacement pump that use one or more rotating screws to move fluid along the axis of the screw. These pumps are highly effective at handling viscous liquids, including oils, sludges, and even solid-laden slurries. The smooth, continuous flow generated by screw pumps makes them ideal for applications where pulsation or vibration must be minimized, such as in hydraulic systems and food processing.
Screw pumps are often used in the oil and gas industry, as well as in wastewater management, because of their ability to handle both high-viscosity fluids and fluids containing solids. Their robust design makes them highly durable and reliable, even under demanding conditions. They are also known for their energy efficiency, as they require less power to operate compared to other types of pumps when handling high-viscosity fluids.
Submersible Pumps
Submersible pumps are designed to operate while fully submerged in the liquid they are pumping. These pumps are used in applications where the fluid is too deep or difficult to access with standard pumps, such as in wells, mines, or underwater settings. Submersible pumps are commonly used for dewatering, wastewater management, and even oil extraction.
One of the key advantages of submersible pumps is their ability to prevent cavitation, a common problem with above-ground pumps that occurs when air bubbles form and collapse in the fluid, causing damage. Because submersible pumps operate underwater, they are less prone to this issue and can pump liquids more efficiently. Additionally, these pumps are designed to be highly durable and corrosion-resistant, making them suitable for handling harsh or contaminated fluids.
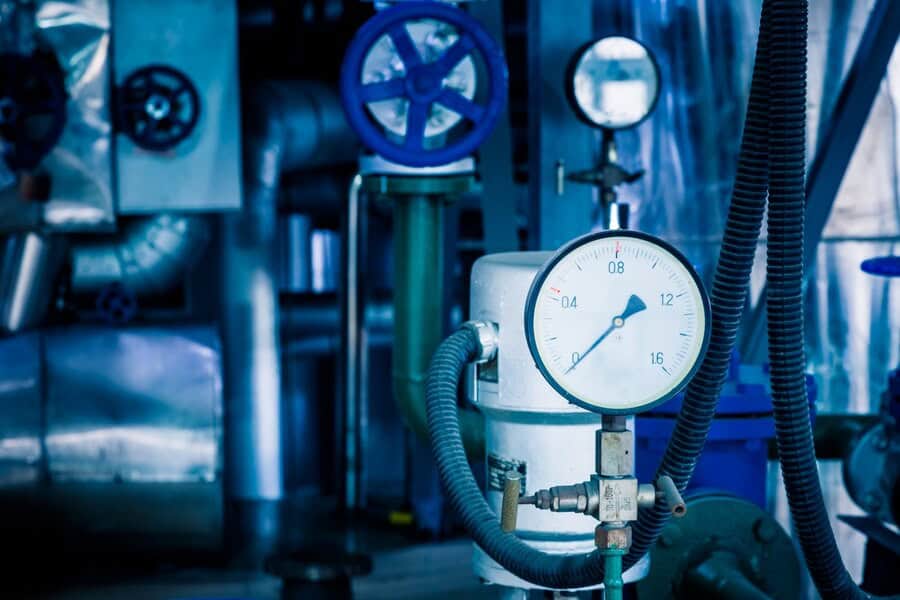
Choosing the right industrial pump depends on various factors, including the type of fluid being handled, the required flow rate, pressure, and the specific application. Whether you need a pump for moving clean water, viscous liquids, abrasive slurries, or hazardous chemicals, understanding the different types of pumps and their specific uses is crucial for optimizing your system’s performance. Pumps such as centrifugal, positive displacement, diaphragm, gear, and submersible pumps all have their own strengths and ideal applications, making it important to match the pump type to your operational needs.
For applications that involve slurries or other challenging materials, exploring options from reputable manufacturers can help ensure that you select the most efficient and reliable pump for the job. With the right pump in place, industrial processes can run smoothly, safely, and efficiently, reducing downtime and operational costs.