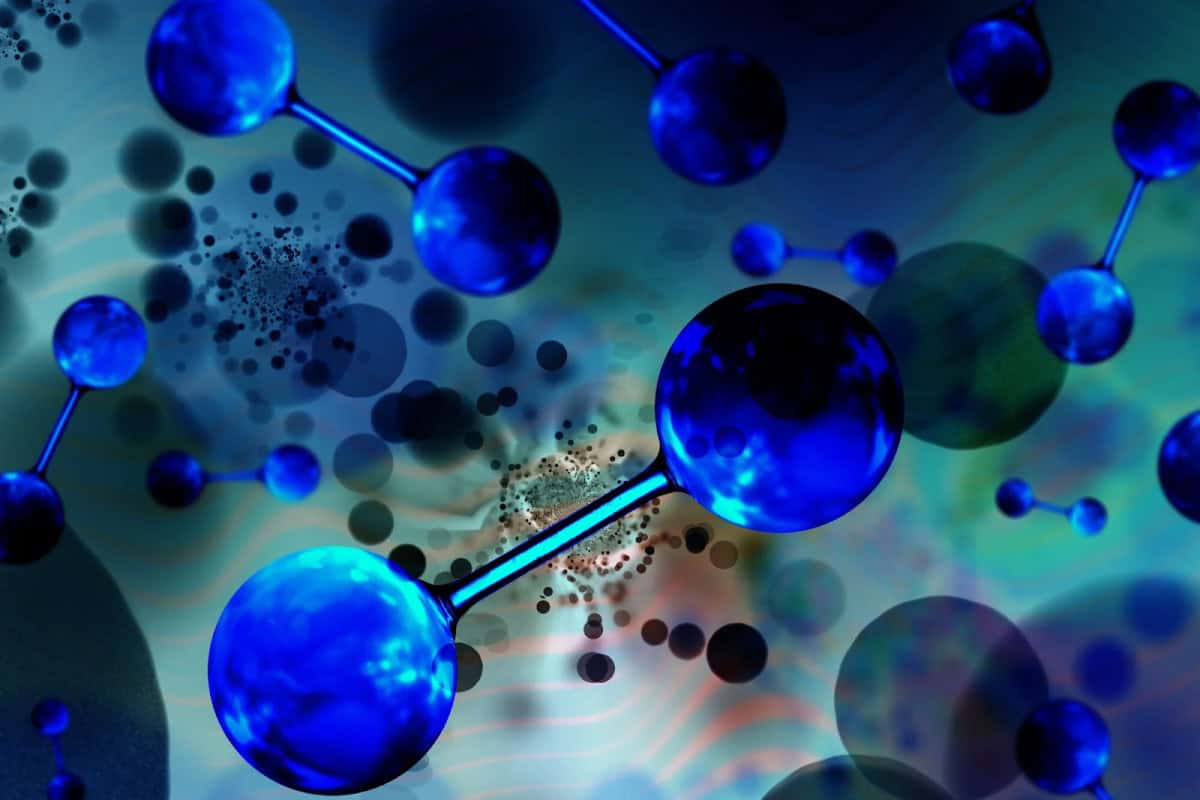
Transformers play a crucial role in the power grid, ensuring that electricity is effectively distributed across networks. However, these devices are prone to faults, many of which are linked to the buildup of hydrogen gas within the transformer oil. When a fault occurs, such as overheating or arcing, it breaks down the oil and produces hydrogen as a byproduct. Monitoring this hydrogen level is essential for detecting potential issues early on, preventing transformer failure, and maintaining the overall reliability of the power grid. Here’s a closer look at why hydrogen monitoring is important, how it works, and the benefits of using innovative solutions.
1. Early Detection of Faults
Hydrogen monitoring is one of the most effective ways to detect faults early in transformers. Electrical faults, such as partial discharges or arcing, can cause a breakdown of the transformer oil, leading to the production of gases, primarily hydrogen. By tracking the amount of hydrogen in the oil, operators can identify emerging issues before they become severe, allowing for timely intervention.
The buildup of hydrogen acts as an early indicator of potential transformer malfunctions, and regular monitoring enables preventive maintenance. With the ability to detect issues early, plant operators can avoid costly repairs and unexpected shutdowns, ensuring transformers remain in optimal working condition.
2. Enhancing Transformer Reliability
A malfunctioning transformer can lead to significant disruptions in power supply, affecting everything from households to industrial facilities. Regular hydrogen monitoring enhances transformer reliability by providing continuous insight into the equipment’s health. When the hydrogen concentration remains stable, it indicates that the transformer is functioning correctly. However, an increase in hydrogen levels signals that immediate attention may be necessary to address underlying issues.
Transformers are critical infrastructure, and by using hydrogen monitoring systems, operators can improve reliability, preventing downtime and ensuring the stability of the power network. Real-time monitoring solutions from H2scan, and other similar companies enable consistent observation. That way, you’ll have a detailed view of the transformer’s condition and give operators the data needed to maintain stable operations.
3. Preventing Costly Repairs and Downtime
Transformer failures can be expensive to repair, particularly when damage extends to the core components or surrounding electrical systems. Even a short period of downtime can lead to operational losses, especially for industrial users who rely on a stable power supply. By monitoring hydrogen levels, companies can take action to prevent minor faults from escalating into major failures, reducing the likelihood of costly repairs.
Proactive hydrogen monitoring is a cost-effective approach to transformer maintenance. Instead of waiting for a fault to develop, operators can address small issues before they worsen, saving both time and resources. Hydrogen monitoring is therefore not only a safety measure but also a financial investment that can significantly reduce overall maintenance costs.
4. Improving Safety for Personnel and Equipment
Transformers operating under faulty conditions pose a risk to both personnel and equipment. Faults such as arcing or overheating can lead to dangerous conditions, including fire or explosion. Monitoring hydrogen levels helps to mitigate these risks by providing an early warning system for abnormal activity, allowing maintenance teams to intervene safely and address the issue before it escalates.
With real-time monitoring, equipment operators can respond quickly to abnormal hydrogen levels, ensuring that potential hazards are managed swiftly. Reliable hydrogen detection solutions improve workplace safety by giving personnel the information they need to prevent hazardous situations, creating a safer environment for everyone involved.
5. Ensuring Compliance with Industry Standards
Hydrogen monitoring in transformers is often part of industry regulations and safety standards. Power utilities and industrial facilities are required to adhere to certain guidelines to maintain the reliability of their equipment and ensure operational safety. Regular monitoring of hydrogen levels is a proactive way to comply with these standards, demonstrating a commitment to best practices and regulatory requirements.
By using advanced hydrogen monitoring solutions, companies can ensure they meet or exceed industry standards for transformer maintenance. Compliance not only boosts the credibility of the business but also ensures smoother operations, avoiding penalties or regulatory challenges that may arise from inadequate monitoring practices.
6. Leveraging Advanced Technology for Precision Monitoring
Recent advances in hydrogen monitoring technology allow for more accurate and reliable detection of gas levels in transformers. Traditional methods of detecting faults, like dissolved gas analysis (DGA), are effective but often require lab testing, which can be time-consuming and limit the ability to act quickly. In contrast, real-time hydrogen monitoring solutions provide immediate insights, enabling quicker responses and better overall transformer management.
Solutions leverage cutting-edge sensors to provide precise hydrogen measurements in real-time. These technologies eliminate the need for frequent oil samples and lab analyses, instead offering continuous, real-time monitoring that helps operators take immediate action when needed. This technology enables plant operators to make faster, data-driven decisions that improve transformer longevity and reliability.
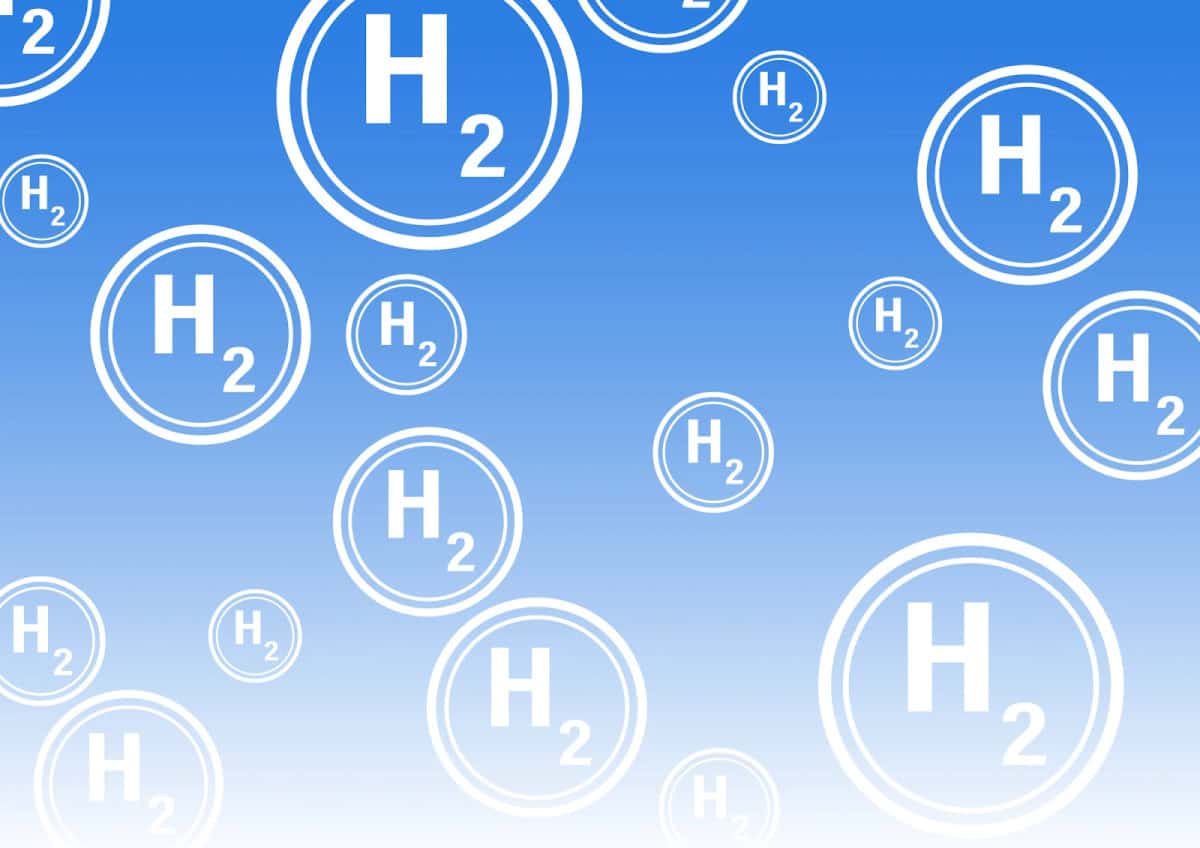
Hydrogen monitoring is a vital component of transformer maintenance, enabling early fault detection, improving reliability, reducing repair costs, and ensuring the safety of both personnel and equipment. By investing in real-time hydrogen monitoring solutions, operators gain valuable insights into transformer health, helping them respond proactively to potential issues and maintain a stable, safe power supply. With advanced monitoring technology, companies can enhance operational efficiency, extend transformer lifespan, and ensure compliance with industry standards, making hydrogen monitoring an essential strategy for effective transformer management.